What Material is Used for Rotary Vanes?
Rotary vanes play a crucial role in various mechanical systems, particularly in vacuum pumps and compressors. Understanding the materials used in their construction is essential for ensuring efficiency, durability, and optimal performance. This article delves into the different materials employed in rotary vanes, their benefits, applications, and future trends in the industry.
Introduction to Rotary Vanes
Rotary vanes are integral components in rotary vane pumps and compressors. These devices rely on the precise movement of vanes to create a vacuum or compress air. The vanes slide within a rotor, maintaining contact with the pump’s housing to regulate airflow and pressure. The choice of material for these vanes significantly impacts the pump’s efficiency, lifespan, and overall performance.
Key Functions of Rotary Vanes:
- Air Compression: Facilitates the compression of air within the pump.
- Vacuum Creation: Generates a vacuum by reducing internal pressure.
- Sealing Mechanism: Ensures airtight operation by maintaining contact with the pump housing.
Understanding the materials used in rotary vanes helps in selecting the right pump for specific applications, whether industrial, automotive, or household.
Common Materials Used in Rotary Vanes
Rotary vanes are crafted from a variety of materials, each offering unique properties that cater to different operational demands. The most common materials include:
1. Carbon
Carbon is widely used due to its excellent wear resistance and self-lubricating properties. Carbon vanes can withstand high temperatures and reduce friction, enhancing the pump’s efficiency and longevity.
2. Stainless Steel
Stainless steel vanes are known for their strength and durability. They are resistant to corrosion and can handle high-pressure environments, making them suitable for industrial applications.
3. Aluminum
Aluminum vanes are lightweight and offer good thermal conductivity. While not as durable as carbon or stainless steel, they are cost-effective and suitable for less demanding applications.
4. Composite Materials
Advanced composite materials combine the benefits of various metals and polymers, providing a balance between strength, flexibility, and resistance to wear and tear.
Comparison of Common Materials:
Material | Durability | Cost | Weight | Corrosion Resistance | Self-Lubricating |
---|---|---|---|---|---|
Carbon | High | Medium | Medium | High | Yes |
Stainless Steel | Very High | High | Heavy | Very High | No |
Aluminum | Medium | Low | Light | Medium | No |
Composite | High | Variable | Variable | High | Yes |
Selecting the appropriate material depends on the specific requirements of the application, including environmental conditions, operational stress, and budget constraints.
Carbon Vanes: Benefits and Applications
Carbon vanes are a popular choice in the rotary vane industry due to their superior performance characteristics. Their unique properties make them ideal for a wide range of applications.
Benefits of Carbon Vanes:
- Wear Resistance: Carbon’s hardness reduces wear and tear, extending the vane’s lifespan.
- Self-Lubricating: Minimizes friction between the vane and the pump housing, enhancing efficiency.
- Thermal Stability: Can operate effectively at high temperatures without degrading.
- Noise Reduction: Carbon materials help in dampening operational noise, providing a quieter performance.
Applications:
- Vacuum Pumps: Ideal for creating high-efficiency vacuums in laboratory and industrial settings.
- Air Compressors: Enhances the performance and durability of compressors used in manufacturing.
- Automotive Systems: Utilized in various automotive components requiring reliable air compression.
“Carbon vanes revolutionize the efficiency of rotary vane pumps, offering unmatched durability and performance,” says Dr. Emily Roberts, a materials science expert.
For more information on carbon vanes, visit our Carbon Vanes section.
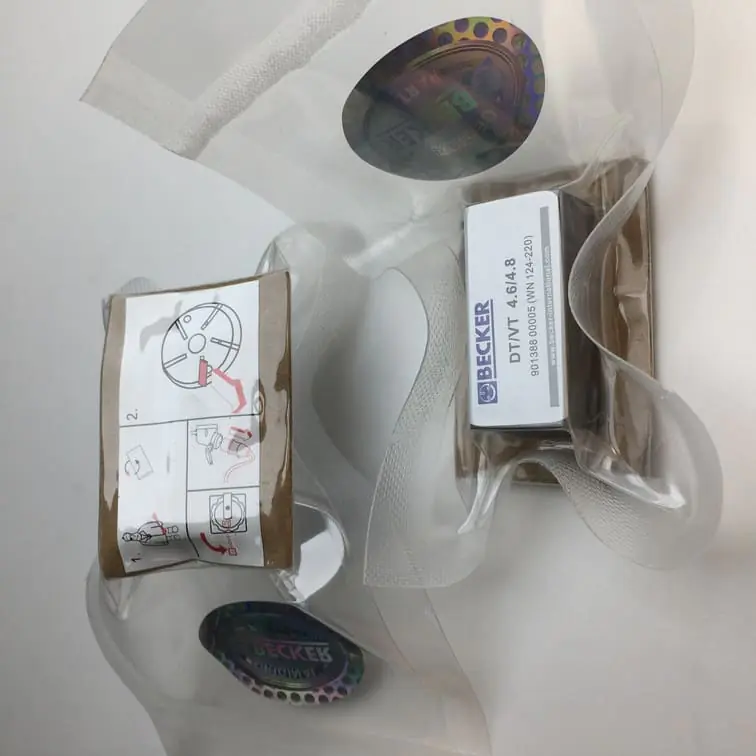
Metal Vanes: Types and Uses
Metal vanes, particularly those made from stainless steel and aluminum, are essential in applications where strength and durability are paramount.
Stainless Steel Vanes:
- High Strength: Capable of handling significant pressure without deforming.
- Corrosion Resistant: Suitable for environments exposed to moisture and chemicals.
- Longevity: Offers a longer lifespan compared to other metal vanes.
Aluminum Vanes:
- Lightweight: Reduces the overall weight of the pump, enhancing energy efficiency.
- Good Thermal Conductivity: Helps in dissipating heat quickly, maintaining optimal operating temperatures.
- Cost-Effective: More affordable than stainless steel, making them ideal for budget-conscious applications.
Applications of Metal Vanes:
- Industrial Compressors: Where high pressure and continuous operation are required.
- Marine Equipment: Resistant to saltwater corrosion, making them suitable for marine environments.
- Heavy Machinery: Ensures reliable performance under strenuous operational conditions.
For a selection of high-quality metal vanes, explore our Vacuum Pump Spare Parts collection.

Composite Materials in Rotary Vane Design
The advancement of composite materials has opened new avenues in the design and functionality of rotary vanes. These materials combine the strengths of multiple substances to create a superior product.
Advantages of Composite Materials:
- Enhanced Durability: Combines the toughness of metals with the flexibility of polymers.
- Lightweight: Reduces the overall weight without compromising strength.
- Customizable Properties: Can be engineered to meet specific operational requirements, such as increased wear resistance or thermal stability.
- Improved Efficiency: Optimizes performance by reducing friction and enhancing sealing capabilities.
Applications:
- High-Performance Compressors: Where efficiency and reliability are critical.
- Aerospace Industry: Lightweight and strong composites are essential for aerospace applications.
- Medical Equipment: Ensures precision and reliability in sensitive medical devices.
Future Prospects:
With ongoing research and development, composite materials are expected to become more prevalent in the rotary vane industry, offering even greater performance enhancements and cost efficiencies.
Factors Influencing Material Selection
Choosing the right material for rotary vanes involves considering several critical factors to ensure optimal performance and longevity.
1. Operational Conditions:
- Temperature: High-temperature environments may require materials with better thermal stability, such as carbon or stainless steel.
- Pressure: Applications involving high pressure necessitate stronger materials like stainless steel.
2. Environmental Exposure:
- Corrosive Environments: Materials like stainless steel and certain composites offer better resistance to corrosion.
- Moisture Levels: High humidity or wet conditions can degrade certain materials, making corrosion-resistant options preferable.
3. Cost Constraints:
Balancing material quality with budget considerations is essential. While carbon and stainless steel offer superior performance, aluminum and composites may provide a cost-effective alternative without significantly compromising quality.
4. Maintenance Requirements:
Materials that are self-lubricating or require less frequent maintenance can reduce operational costs and downtime.
5. Compatibility with Pump Design:
Ensuring that the vane material is compatible with the pump’s design and other components is crucial for seamless operation and longevity.
Table: Material Selection Criteria
Factor | Carbon | Stainless Steel | Aluminum | Composite |
---|---|---|---|---|
Temperature Resistance | High | Very High | Medium | High |
Pressure Handling | High | Very High | Medium | High |
Corrosion Resistance | High | Very High | Medium | High |
Cost | Medium | High | Low | Variable |
Maintenance | Low | Low | Medium | Low |
Selecting the appropriate material based on these factors ensures the rotary vane operates efficiently and lasts longer.
Advantages of Using High-Quality Materials
Investing in high-quality materials for rotary vanes offers numerous benefits that can enhance the performance and reliability of mechanical systems.
1. Increased Durability:
High-quality materials resist wear and tear, reducing the frequency of replacements and maintenance.
2. Enhanced Efficiency:
Materials with low friction properties, such as carbon, improve the overall efficiency of the pump by minimizing energy loss.
3. Better Sealing:
Quality materials ensure a tighter seal between the vane and the pump housing, preventing leaks and maintaining optimal pressure levels.
4. Reduced Noise Levels:
Materials that dampen vibrations contribute to quieter operation, which is beneficial in environments where noise is a concern.
5. Long-Term Cost Savings:
Although high-quality materials may have a higher initial cost, their longevity and reduced maintenance needs lead to significant cost savings over time.
“Choosing the right material for rotary vanes is not just about performance today, but ensuring reliability and efficiency for the future,” states John Martinez, an industrial engineering specialist.
For premium quality rotary vanes, check out our 90138800005 | WN 124-220 Original Becker Set of 5 Vanes product page.
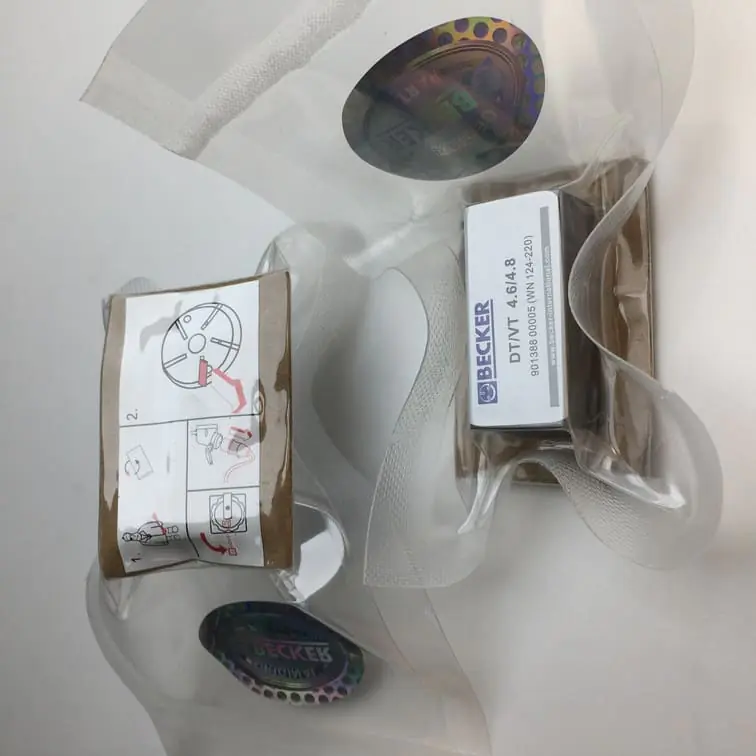
Future Trends in Rotary Vane Materials
The rotary vane industry is continually evolving, with advancements in material science driving innovation and improved performance.
1. Nanomaterials:
Incorporating nanotechnology into vane materials can enhance strength, reduce weight, and improve thermal properties, leading to more efficient pumps.
2. Sustainable Materials:
With a growing emphasis on sustainability, there is a shift towards using eco-friendly materials that offer high performance without harming the environment.
3. Smart Materials:
Materials that can adapt to changing operational conditions, such as temperature and pressure, are being developed to create more versatile and resilient rotary vanes.
4. Enhanced Composites:
Ongoing research is leading to the creation of advanced composites that offer superior properties, such as increased wear resistance and flexibility, further boosting vane performance.
5. 3D Printing:
Additive manufacturing techniques like 3D printing allow for the creation of complex vane designs that were previously impossible, enabling more efficient and customized solutions.
Future Outlook:
As technology progresses, the materials used in rotary vanes will continue to advance, offering greater efficiency, durability, and adaptability to meet the evolving needs of various industries.
FAQs
1. What are the primary materials used for rotary vanes?
Rotary vanes are primarily made from carbon, stainless steel, aluminum, and composite materials. Each material offers unique benefits depending on the application requirements.
2. Why are carbon vanes preferred in vacuum pumps?
Carbon vanes are preferred due to their excellent wear resistance, self-lubricating properties, and ability to operate efficiently at high temperatures, enhancing the pump’s overall performance.
3. Can rotary vanes made of aluminum withstand high-pressure environments?
While aluminum vanes are lightweight and cost-effective, they are generally better suited for low to medium-pressure applications. For high-pressure environments, materials like stainless steel are more appropriate.
4. How do composite materials improve rotary vane performance?
Composite materials combine the strengths of various substances, offering enhanced durability, flexibility, and resistance to wear and tear. This results in improved efficiency and longer vane lifespan.
5. What factors should be considered when selecting vane materials?
Factors include operational conditions (temperature and pressure), environmental exposure, cost constraints, maintenance requirements, and compatibility with the pump design.
6. Are there any sustainable material options for rotary vanes?
Yes, the industry is moving towards eco-friendly and sustainable materials that provide high performance while minimizing environmental impact.
Conclusion
Selecting the right material for rotary vanes is pivotal in ensuring the efficiency, durability, and reliability of pumps and compressors. From the wear-resistant properties of carbon to the strength of stainless steel and the versatility of composite materials, each option offers distinct advantages tailored to specific applications. As the industry advances, the integration of innovative materials promises to enhance performance further, catering to the evolving demands of various sectors. By understanding the characteristics and benefits of each material, manufacturers and consumers can make informed decisions that lead to optimized performance and long-term cost savings.
For more information on rotary vanes and related products, explore our extensive Vacuum Pump Spare Parts collection and find the perfect fit for your needs.