Carbon Vanes: Material Science, Function, and Industrial Benefits
1. Introduction: Understanding Carbon Vanes
Carbon vanes are precisely engineered components, typically appearing as rectangular blades, that play a critical role in the operation of various types of pumps and compressors, most notably rotary vane designs. Manufactured primarily from specialized carbon graphite materials, these vanes are fundamental to the mechanism that generates vacuum or pressure within these machines.
The fundamental purpose of a carbon vane is to function as a dynamic seal within a pump or compressor. Installed in radial slots within a rotating cylinder (rotor), the vanes slide outwards to maintain contact with the inner wall of the pump housing (stator or casing). This action creates sealed, variable-volume chambers between the rotor, vanes, and housing. As the rotor turns, these chambers trap, transport, and progressively compress (in a compressor) or expand (creating vacuum in a pump) the working fluid, which can be a gas or a liquid. This mechanism classifies rotary vane devices as positive displacement pumps.
A defining characteristic and major driver for the widespread use of carbon vanes is their suitability for dry-running o oil-less vacuum pumps and compressors. The inherent properties of carbon graphite, particularly its self-lubricating nature, allow these pumps to operate effectively without the need for oil lubrication within the pumping chamber. This capability is crucial in applications where oil contamination of the process fluid or the environment is unacceptable, such as in the food and beverage, medical, pharmaceutical, and printing industries. Therefore, carbon vanes are not merely components but are often the enabling elements that make oil-free pump technology viable and highly valuable in specific markets. The material choice itself is foundational to the core value proposition of these pumps.
This blog will provide a comprehensive analysis of carbon vanes, exploring the material science of carbon graphite that underpins their performance. It will detail their working principle within rotary vane machinery, outline the significant operational benefits they offer, survey their diverse applications across industries, and discuss important considerations for their selection and use.
2. The Science Behind Carbon Vanes: Material Properties Explored
The unique performance characteristics of carbon vanes stem directly from the properties of their primary constituent material: carbon graphite. Understanding this material is key to appreciating the functionality and advantages of the vanes themselves.
2.1 Introduction to Carbon Graphite
Carbon graphite is a composite material primarily composed of carbon atoms, exhibiting properties derived from both amorphous carbon and crystalline graphite. Its production involves several key steps. The process typically begins with carbon-rich raw materials, such as petroleum coke or pitch, which are purified and mixed with binders (like coal-tar pitch). This mixture is then molded into the desired shape (e.g., blocks from which vanes can be machined, or pressed-to-size shapes). Following molding, the shapes undergo a high-temperature baking process, which carbonizes the binder, converting it to carbon and significantly enhancing the material’s strength.
For many grades intended for demanding applications, a further step called graphitization is employed. This involves heating the baked material to even higher temperatures, often between 2500℃and 3000℃. This intense heat treatment transforms the amorphous carbon structure into a more ordered, crystalline graphite structure, enhancing properties like thermal and electrical conductivity, oxidation resistance, and self-lubrication. The resulting carbon graphite material, whether only baked or fully graphitized, typically possesses a degree of inherent porosity (often 10-25% by volume). To tailor the material for specific performance requirements, this porosity is often filled through impregnation processes using various materials like resins, metals, or salts.
2.2 Crucial Properties of Carbon Graphite for Vanes
Several key properties of carbon graphite make it exceptionally well-suited for use as vanes in pumps and compressors:
- Self-Lubrication (Dry-Running Capability): This is arguably the most critical property. Graphite’s crystalline structure consists of layers of carbon atoms arranged in hexagonal lattices. Within each layer (graphene plane), the atoms are strongly bonded. However, the forces between these layers (van der Waals forces) are significantly weaker. This structural anisotropy allows the layers to slide easily over one another, imparting inherent lubricity. During operation, carbon graphite can also deposit a thin, durable transfer film onto the mating surface (the pump housing wall), effectively allowing the vane to run against a layer of its own material, further reducing friction and wear. Adsorbed molecules, like water vapor, can also play a role, although graphite’s lubricity persists even in dry environments. This self-lubricating characteristic eliminates the need for external oil or grease lubrication within the pumping chamber, which is the cornerstone of oil-less pump design. This prevents contamination of the pumped medium and exhaust air, crucial for applications demanding purity, and enables operation in environments where conventional lubrication is impractical or impossible. The low friction also contributes to higher energy efficiency.
- Thermal Characteristics: Carbon graphite exhibits excellent performance across a wide range of temperatures.
- High Thermal Stability: It can withstand continuous high operating temperatures, often up to 315∘C to 455∘C (600∘F to 850∘F) in oxidizing atmospheres (like air), and even higher temperatures (e.g., 500∘C or more, up to 1600∘F for some grades) in neutral or reducing atmospheres, depending on the specific grade and impregnation. Electro Graphitized grades generally offer higher temperature resistance than standard carbon grades.
- Buena conductividad térmica: Carbon graphite conducts heat effectively, which helps dissipate the frictional heat generated at the contact points between the vane tip and the housing wall, preventing localized overheating.
- Low Coefficient of Thermal Expansion (CTE): This is a particularly vital property. Carbon graphite expands and contracts very little with changes in temperature; its CTE is typically about a quarter that of steel. This dimensional stability ensures that the precise clearances designed between the vane, its rotor slot, and the pump housing are maintained throughout the operating temperature range. This prevents the vanes from binding in their slots or losing effective sealing contact with the housing wall, thereby ensuring consistent pump efficiency and reliability.
- Chemical Inertness & Corrosion Resistance: Carbon graphite is highly resistant to chemical attack from a broad spectrum of substances, including most acids (like hydrochloric, sulfuric), alkalis, solvents (like petrol, paraffin), organic compounds, and water (pure or salt). It is generally considered chemically inert. This allows carbon vanes to be used reliably in pumps handling corrosive fluids or operating within harsh chemical processing environments. However, it’s important to note that strong oxidizing agents (e.g., nitric acid, perchloric acid, halogens) can attack carbon graphite, especially at elevated temperatures.
- Mechanical Properties: Carbon graphite provides a robust combination of mechanical characteristics suitable for vane applications.
- Strength and Hardness: It possesses good compressive strength, allowing it to withstand the pressure differentials across the vane, and adequate flexural strength to resist bending forces. It also exhibits good hardness, contributing to its wear resistance.
- Resistencia al desgaste: This is a standout feature, stemming from the self-lubricating nature and hardness. Carbon graphite vanes exhibit low wear rates, especially after an initial bedding-in period during which a transfer film is established. This ensures a long service life and maintains pump performance over time.
- Tailorability and Limitations: The specific mechanical properties can be tailored by adjusting the ratio of amorphous carbon (harder, stronger, higher friction) to graphite (softer, lubricating, weaker) in the formulation, and significantly enhanced through impregnation. While robust, carbon graphite can be more brittle than metals or some fiber-reinforced composites, meaning it may have lower resistance to sudden impacts or shock loads and requires careful handling during installation.
- Dimensional Stability & Non-Toxicity:
- Stability: In addition to low thermal expansion, carbon graphite is dimensionally stable because it is non-hygroscopic, meaning it does not absorb moisture or swell when exposed to water or humid environments. This further contributes to maintaining consistent operating clearances and performance.
- Non-Toxicity: Carbon graphite is inherently non-toxic and cannot contaminate the fluids being handled. Many grades are specifically formulated and certified (e.g., FDA compliant) for use in food processing, beverage handling, medical devices, and pharmaceutical applications where purity and safety are paramount.
2.3 Material Grades and Impregnations
It is crucial to recognize that “carbon graphite” is not a single material but rather a family of materials engineered for specific performance characteristics. Base grades can vary significantly depending on the raw materials used, the particle size, the ratio of carbon to graphite precursors, and the processing temperatures (baking vs. graphitization).
Furthermore, the inherent porosity of baked or graphitized carbon is almost always addressed through impregnation – the process of filling the pores with another material to enhance specific properties. Common impregnants and their effects include:
- Synthetic Resins (e.g., Phenolic, Epoxy): These are widely used to increase mechanical strength (compressive and flexural), improve wear resistance, and significantly reduce permeability, making the material impervious and suitable for sealing applications. Resin-impregnated grades are often selected for food, beverage, and pharmaceutical applications due to their inertness and potential for FDA compliance. However, the organic nature of resins typically limits the maximum continuous operating temperature to around 200∘C to 260∘C (392∘F to 500∘F). Examples include ANSTAC M105K and Assam Carbon HYX67.
- Antimony: Impregnation with this metal significantly increases mechanical strength, hardness, and thermal conductivity. Antimony-filled grades are often used in applications involving higher loads, hot water, or steam, and can typically operate at higher temperatures (up to around 450∘C or 842∘F) than resin-filled grades.
- Other Metals (Copper, Silver, Babbitt): These impregnants dramatically increase strength, thermal conductivity, and particularly electrical conductivity. They are typically used for specialized applications requiring high pressure capability or electrical current transfer, rather than standard pump vanes.
- Mineral Salts / Phosphates (Oxidation Inhibitors): These impregnants are added to enhance the material’s resistance to oxidation at very high temperatures, extending the operational ceiling in air beyond that of standard or even graphitized grades (potentially up to 538∘C / 1000∘F or higher for specific formulations).
- Carbon: Re-impregnating with carbon (e.g., pyrolytic carbon) can further reduce porosity while maintaining excellent chemical resistance, making these grades suitable for highly corrosive environments.
- PTFE / Fluorides (Film Formers): These impregnants enhance the self-lubricating properties, particularly beneficial in extremely dry gas applications, vacuum environments, or cryogenic conditions where even trace moisture for boundary lubrication is absent.
The existence of these diverse grades and impregnations demonstrates that carbon graphite materials are deliberately engineered and selected to meet specific application demands. Manufacturers like St. Marys Carbon , Mersen (JP grades) , SGL Carbon (SIGRAFINE grades like EK2230, V2048) , and Helwig Carbon offer proprietary formulations tailored for optimal performance in various operating conditions.
However, this tailoring often involves trade-offs. For example, increasing the proportion of amorphous carbon enhances hardness and strength but may slightly reduce lubricity compared to a higher graphite content material. Similarly, resin impregnation boosts strength and impermeability but imposes a lower temperature limit compared to metal or salt impregnations. Therefore, selecting the appropriate carbon graphite grade for a vane application requires careful consideration of the primary performance requirements (e.g., temperature resistance, chemical compatibility, required strength, purity) and optimizing the material choice accordingly.
Table 1: Representative Properties of Carbon Graphite Grades for Vane Applications
Propiedad | Unit | General Carbon Graphite | Resin Impregnated | Antimony Impregnated | High Temp / Electrographite |
Apparent Density | g/cm³ (lbs/ft³) | 1.70-1.80 (106-112) | 1.75-1.85 (109-115) | >1.9 (>119) | 1.75-1.85 (109-115) |
Hardness (Scleroscope / Shore) | – | 40-85 (Sclero) | 85-100 (Sclero) | >90 (Sclero) | 65-95 (Sclero) |
Compressive Strength | MPa (psi) | 55-208 (8k-30k) | 145-300 (21k-43k) | >200 (>29k) | 145-250 (21k-36k) |
Flexural Strength | MPa (psi) | 28-62 (4k-9k) | 50-75 (7k-11k) | >60 (>8.7k) | 40-70 (5.8k-10k) |
Coefficient of Thermal Expansion | 10−6/∘C (10−6/∘F) | 2.5-4.5 (1.4-2.5) | 2.5-4.5 (1.4-2.5) | ~4.0-5.0 (~2.2-2.8) | 2.0-4.0 (1.1-2.2) |
Thermal Conductivity | W/m·K | 5-15 | 5-15 | >15 | 15-85+ |
Max Operating Temp (Oxidizing) | ∘C (∘F) | 315-455 (600-850) | ~200-260 (~400-500) | ~350-450 (~660-840) | 450-600+ (840-1112+) |
Chemical Resistance (General) | – | Excelente | Excelente | Good-Excellent | Excelente |
Autolubricación | – | Good-Excellent | Good-Excellent | Bien | Excelente |
Notes: Values are typical ranges and vary significantly between specific grades and manufacturers. Consult manufacturer data for specific grades. Chemical resistance depends on resin type and specific chemical. Temperature limits are approximate and depend on atmosphere and specific grade/impregnant. Data synthesized from.
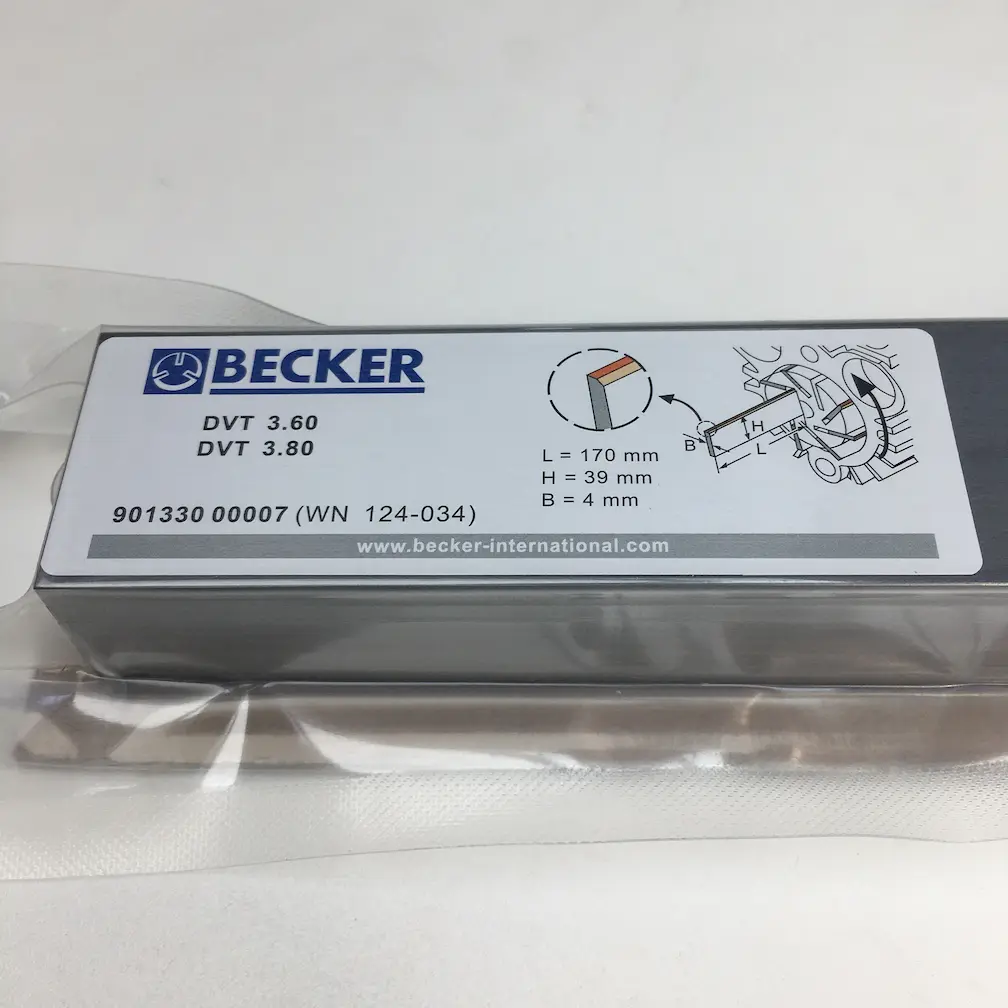
3. How Carbon Vanes Work: Function in Rotary Vane Pumps & Compressors
Carbon vanes are integral to the operation of rotary vane pumps and compressors. Their function is intrinsically linked to the mechanical design of these devices.
3.1 Rotary Vane Pump/Compressor Mechanism
The core components of a typical rotary vane pump or compressor are a cylindrical housing (also called the stator, casing, or pumping ring), a rotor mounted eccentrically (off-center) within this housing, and several flat, rectangular vanes fitted into radial slots machined into the rotor.
The operational cycle proceeds as follows:
- Rotation and Vane Extension: As the driveshaft turns the rotor, centrifugal force acts on the vanes, causing them to slide radially outward within their slots. In some designs, springs or push rods connecting opposing vanes may assist in ensuring the vanes maintain contact with the inner surface of the cylindrical housing, especially at lower speeds or during startup.
- Chamber Formation: The eccentrically positioned rotor and the extended vanes divide the crescent-shaped space between the rotor and the housing into a series of distinct chambers, the volume of which changes as the rotor rotates.
- Intake (Suction): As the rotor turns, the volume of the chambers expanding after passing the point of closest approach between rotor and housing increases. When these expanding chambers pass the inlet port, the resulting decrease in pressure draws the process fluid (gas or liquid) into the pump.
- Transport and Compression/Expansion: The trapped volume of fluid within each chamber is then carried around the casing by the rotating vanes. Due to the rotor’s eccentricity, the volume of these chambers decreases as they approach the discharge port. This reduction in volume compresses the fluid (in a compressor or vacuum pump operating above atmospheric pressure). In a vacuum pump pulling below atmospheric pressure, the initial expansion creates the vacuum, and the subsequent volume reduction moves the evacuated gas towards the outlet.
- Discharge (Exhaust): As the chambers reach their minimum volume near the outlet port, the compressed fluid is forced out through the discharge opening. In oil-sealed pumps, an exhaust valve often prevents backflow, while in dry pumps, the sealing action of the subsequent vane typically fulfills this role.
3.2 The Crucial Role of the Vane
Within this mechanism, the vanes serve as the primary dynamic sealing elements. Their ability to perform two simultaneous actions is critical for efficient operation: they must slide freely in and out of the rotor slots while simultaneously maintaining a continuous, effective seal against the inner wall of the housing.
The unique properties of carbon graphite directly enable this demanding function, particularly in dry-running pumps:
- Autolubricación: Allows the vanes to glide smoothly within the rotor slots and against the housing wall without binding or excessive friction, even in the complete absence of liquid lubrication. This minimizes energy loss and prevents heat buildup from friction.
- Resistencia al desgaste: Ensures that the vanes maintain their precise dimensions and sealing edges despite the continuous sliding contact under load (from pressure differentials and centrifugal force). This translates to consistent performance and long service life.
- Dimensional Stability (Low CTE): Guarantees that the vanes fit correctly within their slots and maintain the necessary contact pressure against the housing wall across the full range of operating temperatures. This prevents issues like excessive leakage (if clearances become too large) or binding (if clearances become too small).
The synergy between the rotary vane mechanism and the properties of carbon graphite is particularly evident in dry pump designs. Without oil to provide lubrication and sealing, conventional materials would likely fail rapidly due to high friction and wear. Carbon graphite’s inherent characteristics directly overcome these challenges, making the oil-less rotary vane pump a viable and highly effective technology. The material properties are not merely compatible with the mechanism; they are fundamentally enabling.
3.3 Dry vs. Lubricated Operation
It’s important to distinguish between two main types of rotary vane pumps based on their lubrication method:
- Dry-Running (Oil-Less) Pumps: These pumps rely entirely on the self-lubricating properties of the carbon graphite vanes for operation. They deliver an oil-free output, which is essential for contamination-sensitive applications.
- Oil-Sealed (Lubricated) Pumps: In these pumps, a circulating oil supply serves multiple functions: lubricating moving parts (including vane tips and rotor bearings), helping to seal the clearances between the vane tips and the housing wall, filling dead volumes to improve efficiency, and removing the heat generated during compression. While carbon graphite vanes are the hallmark of dry pumps, some oil-sealed pumps may utilize vanes made from composite materials, such as fiberglass vanes wrapped with carbon fiber. These composite vanes are chosen for enhanced durability, resistance to harsh chemicals, or ability to tolerate high temperatures within the oil-lubricated environment, preventing oil penetration into the vane core.
Additionally, carbon graphite vanes are sometimes used in pumps designed to handle liquids (“wet running”). In these cases, the pumped liquid itself may provide some degree of lubrication between the vane and the housing, complementing the self-lubricating nature of the carbon graphite.
4. The Advantages: How Carbon Vanes Can Benefit Your Operations
The unique combination of material properties and functional role translates into several significant advantages for users of equipment employing carbon vanes, particularly in dry-running pumps and compressors. These benefits directly impact operational efficiency, reliability, process integrity, and overall cost-effectiveness.
4.1 Key Advantages Elaborated
- Operational Efficiency:
- Reduced Energy Consumption: The inherent low friction of self-lubricating carbon graphite minimizes the energy required to overcome resistance as the vanes slide against the housing and within their slots. This leads to lower power consumption compared to pump designs with higher inherent friction or those requiring energy-consuming auxiliary lubrication systems.
- High-Speed Operation: Carbon graphite’s thermal stability, good thermal conductivity, and wear resistance allow pumps to operate reliably at high rotational speeds. This enables the design of compact pumps that deliver high flow rates relative to their physical size.
- Smooth, Low-Pulsation Output: Rotary vane pumps, facilitated by the consistent sealing of the vanes, generally provide a smooth and relatively pulse-free flow of the pumped medium.
- Reliability and Longevity:
- Extended Vane Life: The excellent wear resistance of carbon graphite translates directly into a long operational lifespan for the vanes, significantly longer than many alternative materials under similar conditions. This means less frequent need for replacement. Some suppliers claim lifetimes several times longer than competitors’ vanes.
- Reduced Maintenance Requirements: In dry-running pumps, the self-lubricating nature eliminates all tasks associated with oil lubrication, such as level checks, oil changes, filter replacements, and oil disposal. Maintenance is often reduced to periodic vane inspection and replacement, which is typically a straightforward process.
- Mayor durabilidad: The material’s good compressive strength and overall robustness contribute to the pump’s ability to withstand operational stresses and maintain performance over time.
- Process Purity and Environmental Benefits:
- Oil-Free Output: This is a primary driver for using carbon vanes in many industries. The absence of oil lubrication in the pumping chamber guarantees that the process gas or air delivered is free from oil contamination. This is non-negotiable in applications like food and beverage production, medical and dental equipment, pharmaceutical manufacturing, laboratory analysis, and printing.
- Material Inertness and Non-Toxicity: Carbon graphite itself does not react with or leach harmful substances into the pumped fluid, ensuring product purity. Many grades meet stringent regulatory standards (e.g., FDA) for contact with consumables.
- Environmental Considerations: Eliminating oil lubrication in dry pumps avoids the environmental concerns and costs associated with used oil disposal. The reduced energy consumption also contributes to a smaller environmental footprint. (Note: The generation of fine graphite dust in dry pumps is a potential environmental/process consideration in some ultra-sensitive cases).
- Versatility and Robustness:
- Wide Operating Temperature Range: Carbon graphite vanes can function reliably in applications ranging from cryogenic temperatures up to several hundred degrees Celsius, depending on the specific grade and atmosphere.
- Broad Chemical Compatibility: Their resistance to most chemicals allows them to be used for pumping a wide variety of gases and liquids, including many that would corrode metals or degrade other materials.
- Suitability for Dry or Wet Conditions: While ideal for dry-running pumps, carbon vanes can also operate effectively in pumps handling liquids, where the fluid may provide supplementary lubrication.
- Excellent Thermal Shock Resistance: The material’s low CTE and good thermal conductivity allow it to withstand rapid changes in temperature without cracking or failing.
- Cost-Effectiveness (Total Cost of Ownership):
- While the initial purchase price of carbon vanes varies depending on grade, size, and supplier, evaluating their cost-effectiveness requires considering the total cost of ownership over the pump’s lifecycle.
- Lower Energy Costs: Resulting from reduced friction.
- Reduced Maintenance Expenditures: Due to longer vane life, elimination of oil and associated labor in dry pumps, and often simpler maintenance procedures.
- Minimized Production Downtime: Increased reliability and less frequent maintenance lead to greater machine uptime and productivity.
- When these factors are combined, carbon vanes often provide a lower total cost of ownership compared to alternatives, especially in applications where their unique benefits are highly valued.
The significance of these advantages, however, is highly dependent on the specific operational context. For instance, in the food and pharmaceutical industries, the paramount benefit is the prevention of oil contamination enabled by the self-lubricating, non-toxic nature of carbon graphite. Conversely, in high-temperature industrial processes, thermal stability and low thermal expansion become the critical factors driving adoption. For handling aggressive chemicals, inertness is key, while for high-duty cycle machinery, longevity and low maintenance offer the greatest value. Assessing the benefits requires matching the vane’s strengths to the specific challenges and priorities of the user’s application.
4.2 Comparative Overview with Alternative Vane Materials
While carbon graphite is a dominant material for vanes, especially in dry pumps, other materials are sometimes used:
- Plastic Vanes (e.g., PEEK, PTFE): Materials like Polyphenylene Sulfide (PPS), Polytetrafluoroethylene (PTFE), or Polyetheretherketone (PEEK) are sometimes used for vanes. They offer good chemical resistance and low friction. Some manufacturers recommend plastic vanes specifically for operation in humid environments due to better moisture tolerance compared to some carbon grades. However, carbon graphite components generally offer improved performance, including reduced leakage (due to tighter possible tolerances), better sound quality (lower noise), and often higher temperature limits and wear resistance.
- Fiber-Reinforced Plastic (FRP) Vanes: These composites use a polymer matrix (like epoxy or polyester) reinforced with fibers (commonly glass fibers). FRP vanes offer good strength-to-weight ratio, excellent corrosion resistance to certain chemicals, and are relatively lightweight and potentially more cost-effective than carbon graphite or carbon fiber composites. They can also be molded into complex shapes. However, their primary limitation is typically lower thermal stability compared to carbon graphite, restricting their use in high-temperature applications. They are often chosen for specific chemical resistance needs or where weight reduction is a primary goal.
- Carbon Fiber Composite Vanes: It is important to distinguish these from solid carbon graphite vanes. Carbon fiber composite vanes typically consist of carbon fibers embedded in a polymer resin matrix, or sometimes a fiberglass core wrapped with carbon fiber layers.
- Properties: These composites offer exceptional stiffness, high tensile strength, low density (lightweight), and excellent fatigue resistance. The carbon fiber wrapping on a fiberglass core is specifically noted for preventing oil penetration, tolerating high temperatures, and resisting corrosive environments, making it suitable for harsh chemical or metalizing applications, often within sellado con aceite pumps.
- Aplicaciones: Due to their high strength and stiffness, they are suited for high-speed, high-stress applications, including advanced industrial pumps, motors, and aerospace components.
- Costo: The manufacturing process for carbon fiber composites is generally more complex and expensive than for solid carbon graphite or FRP.
- Clarification: While sharing the “carbon” name, these composite materials differ significantly from solid carbon graphite. They rely on the strength of the fibers and matrix, not primarily on the inherent self-lubricating properties of graphite, although the carbon fiber itself has relevant characteristics. They are often used where structural integrity under high stress or in specific harsh (often lubricated) environments is the main requirement, whereas solid carbon graphite vanes excel due to their self-lubrication in dry-running conditions.
Table 2: Comparative Overview of Common Vane Materials
Característica | Solid Carbon Graphite | Fiber-Reinforced Plastic (FRP) | Carbon Fiber Composite |
Primary Material | Carbon & Graphite | Polymer Matrix + Glass/Other Fibers | Polymer Matrix + Carbon Fibers |
Key Advantage | Self-Lubrication (Dry Running) | Corrosion Resistance, Cost, Moldability | High Strength/Stiffness, Lightweight |
Autolubricación | Excelente | Poor (Requires Lubrication) | Poor (Requires Lubrication) |
Max Temperature | High (315-600+°C, grade dependent) | Moderate-Low | High (Resin Dependent) |
Strength/Stiffness | Good-Very Good | Bien | Excelente |
Resistencia a la corrosión | Excellent (Broad) | Excellent (Specific Chemicals) | Very Good (Resin Dependent) |
Resistencia al desgaste | Excelente | Moderado | Very Good |
Brittleness | Moderado | Bajo | Bajo |
Aplicaciones típicas | Dry Vacuum Pumps/Compressors, Chemical, Food/Med | Specific Chemical Pumps, Fans | High-Stress/Speed Pumps, Aerospace, Oil-Sealed Pumps (Wrapped) |
Relative Cost | $$ | $ | $$$ |
Notes: Properties are generalized; specific grades vary. While carbon fiber itself has low friction, composites rely on matrix and design, often used in lubricated systems. Cost indication is relative. Data synthesized from.
5. Applications Across Industries
The unique and advantageous properties of carbon graphite vanes have led to their adoption across a remarkably wide range of industries and applications. Their ability to provide reliable, contamination-free operation makes them indispensable in many processes. The breadth of use underscores their status not as a niche product, but as a standard, proven technology for demanding vane pump and compressor applications.
Key application areas include:
- Printing Industry: Widely used in air pumps for printing presses, post-press equipment (e.g., folding, binding machines), paper handling systems, and paper counting equipment. The primary driver is the need for clean, oil-free compressed air or vacuum to avoid contaminating paper stock and printed products. Reliability and low maintenance are also crucial in high-volume printing operations.
- Medical, Pharmaceutical, and Laboratory: Applications include medical and dental vacuum systems, breathing air supplies, laboratory vacuum filtration and drying, centrifuges, gas analyzers, particle counters, and equipment for pharmaceutical research and development. Here, the absolute requirement for oil-free operation, non-toxicity, chemical inertness (for handling various reagents or samples), and high reliability are paramount. Quiet operation can also be a factor in lab and clinical settings.
- Food and Beverage Processing and Packaging: Essential for vacuum packaging machines (extending shelf life), beverage dispensing systems (carbonation, transfer), pumps handling food products, and general food processing equipment. Stringent hygiene standards demand non-toxic, non-contaminating materials compatible with food products and cleaning agents. Carbon vanes meet these needs perfectly due to their inertness and oil-free operation.
- Industrial Automation and Manufacturing: Used extensively in vacuum handling systems for pick-and-place robots, vacuum lifting devices, and vacuum hold-down tables (e.g., in CNC machining, woodworking). Also found in vacuum forming processes and general industrial vacuum or compressed air supplies where oil-free operation is preferred for cleanliness or process compatibility. Durability and reliability are key in these demanding production environments.
- Environmental Engineering: Applications include aeration systems for ponds and wastewater treatment facilities, air sampling equipment for environmental monitoring, gas analyzers, and particle counters. Reliability, the ability to handle continuous air or gas flows, and sometimes resistance to moisture or contaminants are important factors.
- Chemical Industry: Used in pumps and compressors for transferring various chemicals and generating process vacuum. The broad chemical inertness and corrosion resistance of carbon graphite are the primary advantages here, although specific compatibility must always be verified for the chemical being handled and the vane grade used.
- Automotive and Fuel Transfer: Found in fuel transfer pumps (handling petrol, diesel), fuel tank venting systems, fuel meters, and potentially in air supply systems for applications like oil burner air atomizing or brake boosters. Self-lubrication is critical when handling low-lubricity fuels, and material compatibility with fuels is essential.
- Other Applications: Carbon vanes are also utilized in diverse equipment such as spray paint systems, drink vending machines, de-soldering equipment, lamination presses, textile machinery, and various specialized compressors and vacuum pumps.
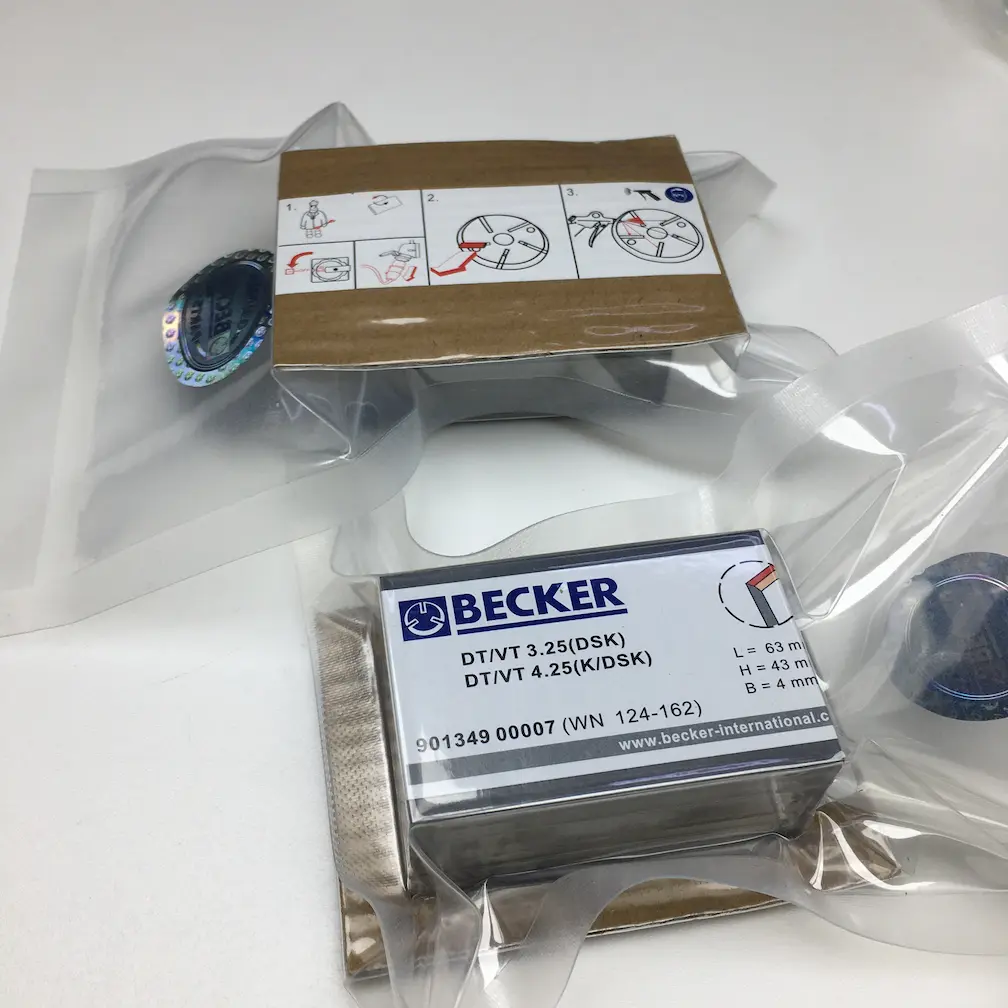
6. Considerations and Conclusion
While carbon graphite vanes offer significant advantages, users should be aware of certain considerations and potential limitations to ensure optimal performance and longevity.
6.1 Potential Limitations and Trade-offs
- Brittleness and Impact Sensitivity: Although possessing good compressive strength, carbon graphite is inherently more brittle than ductile metals or many polymer composites. This necessitates careful handling during storage, transport, and particularly installation to avoid chipping or cracking. Vanes should not be dropped or subjected to sharp impacts. Correct installation procedures, such as ensuring proper chamfer direction, are crucial to prevent premature failure. This characteristic might also limit their suitability in applications involving extremely high shock loads.
- Graphite Dust Generation: In dry-running pumps, the natural wear process that enables self-lubrication inevitably generates fine graphite dust particles. This dust mixes with the pumped gas and is typically discharged with the exhaust. While carbon graphite is non-toxic and inert, this dust may be undesirable in ultra-clean environments or applications where any particulate matter is detrimental. In such cases, downstream filtration of the exhaust gas might be necessary.
- Abrasive Media Handling: Rotary vane pumps with carbon vanes are generally not suitable for pumping fluids containing abrasive solids. Abrasive particles would rapidly accelerate wear on the vane tips and the pump housing, quickly degrading performance and component life.
- High Viscosity Liquids: While capable of pumping low-to-medium viscosity liquids, rotary vane pumps can struggle with highly viscous fluids. High viscosity can impede the free sliding motion of the vanes in their rotor slots, reducing pumping efficiency. Heating jackets may sometimes be used to reduce viscosity and improve pumpability.
- Chemical Compatibility Limits: Despite broad chemical resistance, carbon graphite is susceptible to attack by strong oxidizing agents, particularly at elevated temperatures. Compatibility should always be verified with the specific chemical, concentration, temperature, and vane grade (including impregnant) being considered.
6.2 Importance of Proper Selection, Installation, and System Maintenance
Achieving the full benefits of carbon vanes depends heavily on selecting the correct material grade and ensuring proper installation and system maintenance.
- Grade Selection: As detailed in Section 2.3, numerous carbon graphite grades and impregnations exist. Choosing the optimal vane requires matching the material properties to the specific operating conditions: temperature range, pressure differential, chemical environment, required purity level, rotational speed, and expected mechanical loads. Consulting with vane manufacturers or specialized suppliers (e.g., Becker, Busch, Rietschle, Helwig Carbon, St. Marys Carbon, Mersen, SGL Carbon, Precision Plus, SuperVane) is highly recommended to ensure the selected grade meets the application’s demands.
- Installation Procedures: Correct installation is vital for performance and longevity. This includes thoroughly cleaning the pump rotor slots and housing cavity, ensuring the housing wall is smooth and free from scoring or damage (poor quality vanes can damage the wall), and installing the vanes with the correct orientation (e.g., observing chamfer direction). Incorrect installation can lead to rapid vane breakage or poor pump performance.
- System Condition and Maintenance: The performance and lifespan of carbon vanes are also influenced by the overall condition of the pump system. Worn rotor slots or a scored/damaged housing wall will accelerate vane wear. Furthermore, proper maintenance of other pump components, such as regularly lubricating rotor bearings (using appropriate high-temperature grease) and ensuring air inlet filters are clean and replaced regularly, is essential for reliable pump operation and optimal vane life. Vane performance should be viewed within the context of the entire pump system; neglecting system maintenance can compromise even the highest quality vanes.
6.3 Conclusion
Carbon vanes, crafted from versatile and highly engineered carbon graphite materials, represent a critical technology in modern vacuum and compression systems. Their unique combination of self-lubrication, high thermal stability, broad chemical resistance, excellent wear resistance, and inherent non-toxicity makes them particularly indispensable for dry-running rotary vane pumps and compressors.
These properties translate into tangible benefits for users, including the ability to achieve oil-free operation essential for process purity in sensitive industries, enhanced operational efficiency through low friction and high-speed capability, increased reliability and longevity leading to reduced maintenance and downtime, and robustness across wide temperature ranges and chemical environments. Consequently, carbon vanes have become a standard, enabling component across diverse sectors, from printing and packaging to medical technology and industrial manufacturing.
While considerations such as potential brittleness and dust generation exist, they are often outweighed by the significant advantages offered, particularly when the correct grade is selected for the application and proper installation and system maintenance practices are followed. By understanding the material science, functional principles, benefits, and limitations of carbon vanes, users can effectively leverage this technology to optimize their processes, enhance product quality, and potentially achieve a lower total cost of ownership in demanding applications.